ロジスティクスという言葉が日本で使われる機会が増えてきたのは1990年代からです。バブル崩壊後、大量生産・大量消費のプッシュ型のマーケティングから、少量・多品種・多頻度を前提としたプル型へマーケティングの主流が変化し、ロジスティクスの重要性が高まりました。
物流と同義で扱われることが多いロジスティクスですが、由来が軍事用語の「兵站(へいたん)」だというのは有名な話です。元々は、作戦に従って兵力や用品を確保、管理し、前線へ補給する活動を指していました。そしてそれがマーケティング用語として利用されるようになり、今では一般的なビジネス用語として認識されています。ビジネスの中で、ロジスティクスと物流を使い分ける必要はありませんが、物流業界に従事されている方や物流を経営課題として認識されている方には、ロジスティクスという言葉の意味について理解を深めて頂きたいです。今回のコラムでは、ロジスティクスの基本的な考え方や物流との違い、また、なぜロジスティクスが重要なのかについて説明します。
SCM/3PL/物流のお悩みを解決したい方へ

プロレド・パートナーズでは、現状把握から施策の立案・実行まで一貫したサポートが可能となります。SCM改善について皆様からのご相談をお待ちしております。
ロジスティクスの基本はJust In Time

ロジスティクスとは、調達(仕入れ・生産)から販売(在庫・納品)までの一連の流れを、計画的に管理するプロセス全般を指します。物流の基本的な機能(輸配送、保管、荷役、包装・加工、情報)に加え、需要予測、在庫管理、オーダーフルフィルメントなどがロジスティクスの役割となり、物流を通して顧客のニーズを満たしていくことがロジスティクスの目標です。
これは「必要なものを、必要な時に、必要な数だけ、供給する」というJust In Time(JIT)の考え方と同じで、大きく2つの要素に分けて考えます。1つ目は、需要の把握です。何が、いつ、どこで(誰が)、どれだけ必要かを正確に理解する必要があります。2つ目として、その需要に対する供給をいかに、適正なコストで実現するかです。
1.需要把握のポイント:シナリオ策定
ロジスティクスを考えるとき、イメージされ易いのは供給ですが、需要の正確な把握無くしてロジスティクスの目標達成はありません。販売予測・計画の精度向上が非常に重要となります。一方で、正確な販売計画を策定することは非常に困難です。少しでも精度を高めるために、現状の延長線上として考えるベースケースと売上拡大を目指すための各種施策を考慮したベストケースの2つをシナリオとして準備することが大切です。
2.供給検討のポイント:部分最適から全体最適へ
供給は上述のベースケースから検討します。供給において考えるポイントは、調達/生産、在庫、販売の工程ごとの管理(部分最適)ではなく、調達から販売までの供給プロセス全体に焦点を当てる(全体最適)ことです。調達/生産した製品を、どこで、どれだけ在庫にすることが、需要にマッチし、且つ、コストを最適化できるかを考えます。
このように、需要の把握と供給の実現をより高いレベルへ改善していく活動(マネジメントや手法)がロジスティクスです。
ロジスティクスと物流の違いは?
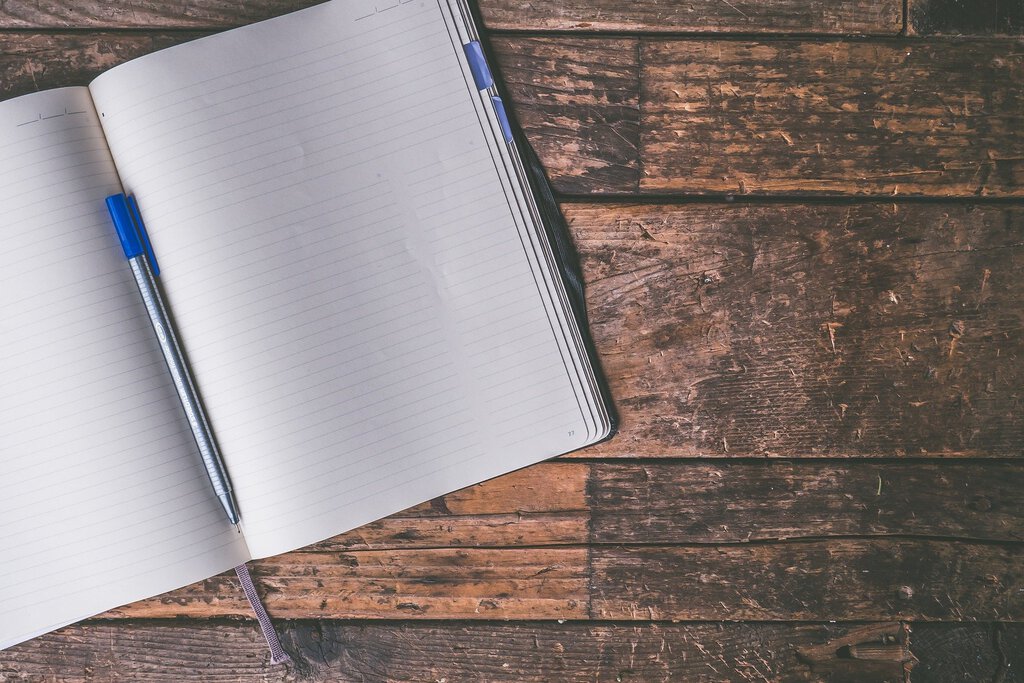
あらためて、物流との違いを見てみましょう。物流という言葉は、1950年代にアメリカのマーケティング用語だったPhysical distribution(物的流通)が日本に入り、日本語に訳されたものです。昨今では英語圏でPhysical distributionという言葉が使用されることは少なく、Logisticsが物流全般を指す意味で使われています。実際、物流という日本語の英訳もLogisticsになります。
物流は「モノを運ぶ」という活動を表した言葉で、ロジスティクスは「マネジメント」に着目した言葉となり、JIS規格の用語定義も以下のようになっています。
物流:JIS Z 0111:2006 1001
物資を供給者から需要者へ、時間的及び空間的に移動する過程の活動。一般的には、包装、輸送、保管、荷役、流通加工及びそれらに関連する情報の諸機能を総合的に管理する活動。調達物流、生産物流、販売物流、回収物流(静脈物流)、消費者物流など、対象領域を特定して呼ぶこともある。
ロジスティクス:JIS Z 0111:2006 1002
物流の諸機能を高度化し、調達、生産、販売、回収などの分野を統合して、需要と供給との適正化を図るとともに顧客満足を向上させ、併せて環境保全、安全対策などをはじめとした社会的課題への対応を目指す戦略的な経営管理。
参照:日本産業規格(JIS)
ロジスティクスの重要性と各企業の取組み

ロジスティクスが適正に行われない場合、過剰在庫によるB/SやC/Fの悪化や、在庫欠品による売上への影響、また、売上に対する物流費比率の上昇といった経営課題が発生します。逆にロジスティクスの適正化が実現できれば、物流費の削減だけでなく、売上拡大への貢献も期待できます。ここでは、ロジスティクスの実践方法をひとつご紹介します。
実践事例:ABC分析を活用した在庫適正化
在庫を総量で捉えるのではなく、ABC分析を活用して、重要度の高いSKUを選定して管理を強化します。調達/生産から倉庫における在庫計上までのリードタイムや倉庫内の保管場所・保管方法、オーダーを受けてから納品までのリードタイムなどについて、重要度の高いSKUへ注力した改善を実施します。重要度の高いSKU(Aランク)とは、全体の10%~20%程度のSKUで、占める売上げが全売上の80%となるような商品です。
ABC分析の例-1

ABC分析を活用する際のポイントは3つあります。1つ目は、自社に適したカテゴライズを行うことです。ABC分析はパレートの法則に関連した考え方ですが、パレートの法則自体は1890年頃に初めて提唱されたもので、消費者の需要が多様化している現代ではこの法則がそのまま当てはまらないケースも多くあります。例えば、「ABC分析の例-1」で記載したAランクでは20%のSKUが80%の売上を作る前提としていますが、実際は20%のSKUが全売上の50%の売上となるケースなどが挙げられます。ABC分析の目的は重点管理ですので、売上の80%となるようにSKUの比率を20%から増やしていくことは間違った考え方です。20%のSKUの売上を拡大に貢献できる、納品L/T短縮や販促強化などの施策を実行します。
2つ目のポイントは、「ABC分析の例-2」のようにSランク商品の設定を検討することです。仮に、全てのSKU数が5,000だとすれば、20%のSKU数は1,000となります。1,000SKUは重点管理の対象としては非常に多いので、5%~10%のSKUをSランクとして新たに設定して、Aランクの中でも最重要SKUとして更なる管理強化を行います。
ABC分析の例-2

3つ目は、一番SKU数の多いCランク商品についてです。SランクとAランク商品に注力した改善を行うことがABC分析の基本ですが、この分析によりCランクであるテール部分についても可視化されています。ロングテールとして意図的に作られたテールなのか、ビジネスの結果として発生したものなのかを明確にすることがポイントです。後者の場合の施策としては、不動在庫の削減を目標とした売切り施策の実施や廃棄の検討を進めます。
まとめ
ロジスティクスは、マネジメント(経営管理)の一環であるという点が物流との大きな違いとなり、最後に挙げた実践方法の施策が物流の範囲を超えた内容であることがご理解頂けたと思います。この実践方法は数あるロジスティクス管理の一例となり、実施すべき施策は業界や企業の戦略により異なります。
プロレド・パートナーズは成果報酬型、且つ、実行支援に強みを持ち、貴社の環境に応じた最適なロジスティクスの構築をご支援いたします。是非、皆様からのご相談をお待ちしております。お気軽にお問い合わせください。
*本コラム内の用語
ABC分析=ABC分析 とは「重点分析」とも呼ばれ在庫管理などで原材料、製品等の資金的重要度を分析する手法
B/S(Balance sheet)=貸借対照表
C/F(Cash flow sheet)=キャッシュフロー計算書
SKU(Stock keeping unit)=倉庫内で管理すべき最小管理アイテム単位
SCM/3PL/物流のお悩みを解決したい方へ

プロレド・パートナーズでは、現状把握から施策の立案・実行まで一貫したサポートが可能となります。SCM改善について皆様からのご相談をお待ちしております。